Fliegen Erklärt: Woher kommt das Bellen beim A320?

Wer schon einmal mit einem Airbus A320 geflogen ist, kennt das Geräusch ganz sicher: Das mysteriöse Hundebellen während des Startens und Herunterfahren der Triebwerke. In diesem Teil der Reihe Fliegen Erklärt schauen wir uns dieses Phänomän genauer an und klären, woher das kommt.
Das Hydrauliksystem des Airbus A320
Das Geräusch kommt aus dem Hydrauliksystem, welches ich an dieser Stelle zunächst grob beschreiben möchte. Da das Hydrauliksystem bei allen Flugzeugen der A320-Familie, also beim Airbus A318, A319, A320 und A321 größtenteils identisch ist, trifft diese Beschreibung natürlich auf alle Flugzeuge der Familie zu. In der Wortwahl beschränke ich mich jedoch auf den Airbus A320.
Ein Airbus A320 hat drei getrennte Hydraulikkreisläufe, welche nach Farben benannt sind: Green, Blue und Yellow. Über diese Hydraulikkreisläufe werden wichtige Systemfunktionen wie Klappen, Ailerons, Spoilers, Ruder, Elevators und Yaw Damper gesteuert. Auch Cargotüren, Bremsen, das Fahrwerk und noch ein paar andere Dinge hängen an den Hydrauliksystemen. Die einzelnen aerodynamischen Steuerflächen werden aus Redundanzgründen von allen drei Kreisläufen angesteuert, aber andere Komponenten wie die Umkehrschubvorrichtungen haben diese Redundanz nicht.
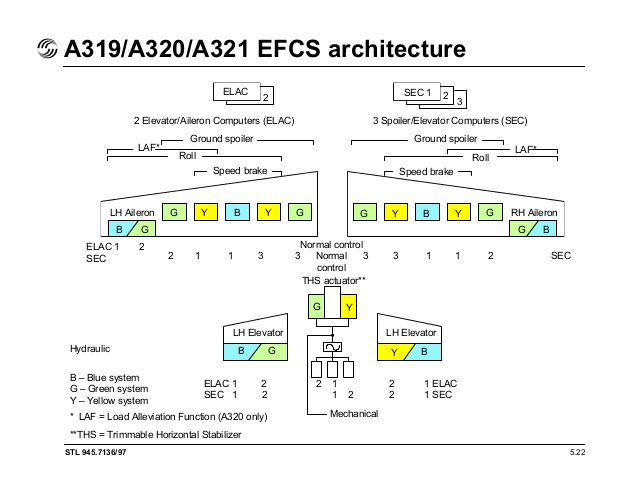
Jedenfalls sind Green und Yellow die Kreisläufe, die durch die Triebwerke bedruckt werden. Das Triebwerk 1 (backbord) betreibt die Pumpe für den grünen Kreislauf und das Triebwerk 2 die Pumpe für den gelben Kreislauf. Der blaue Kreislauf wird durch eine elektrische Pumpe bedruckt und kann im Falle eines Dual Engine Failures durch die Ram Air Turbine im Notfall den Hydraulikdruck aufrecht erhalten und das Flugzeug mit Strom versorgen. Auch das gelbe System hat eine elektrische Pumpe, wozu wir nachher noch einmal kommen. Die Handpumpe im gelben System ist zum manuellen Öffnen der Cargotüren am Boden gedacht.
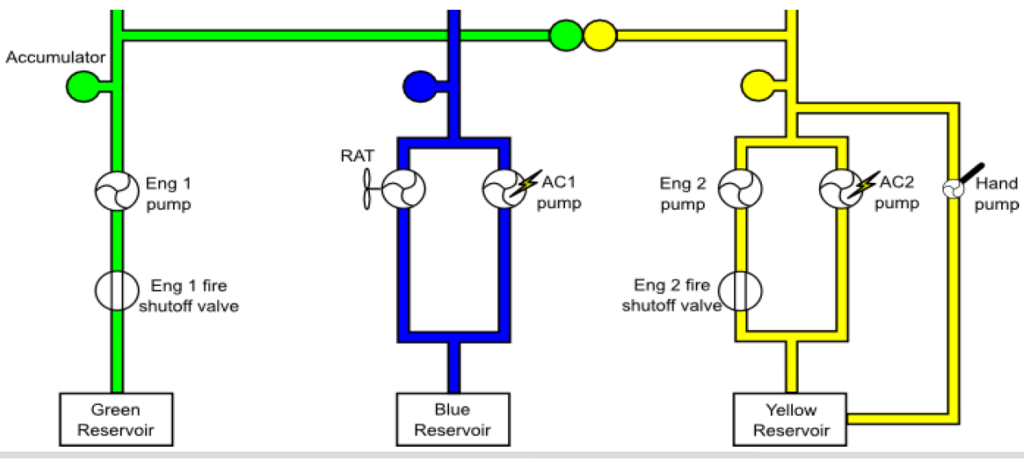
Die Power Transfer Unit (der Hund)
Die drei Systeme operieren wie gesagt unabhängig voneinander, wobei Grün und Gelb aber durch die Power Transfer Unit (PTU) aneinander gekoppelt sind. Die PTU besteht aus zwei über einen Drive Shaft verbundenen Hydraulikpumpen (genauer gesagt zwei Schrägscheiben-Axialkolbenpumpen), die Hydraulikdruck vom gelben auf das grüne System und umgekehrt bringen können. Die Seite mit dem höheren Druck treibt über die entsprechende Pumpe den Drive Shaft, der die Pumpe des anderen Kreislaufs antreibt und so Power überträgt. Zur Funktionsweise dieser Pumpe gibt es hier eine schöne Animation. Wichtig ist, dass keine Hydraulikflüssigkeit ausgetauscht wird. Im Falle eines Druckverlustes auf dem gelben System will man ja schließlich nicht die eventuell für den Druckverlust verantwortliche kontaminierte Hydraulikflüssigkeit auch noch ins gesunde System pumpen. Auch im Falle eines Lecks läuft man so nicht Gefahr, dass beide Kreisläufe wegen einem lokalen Leck komplett auslaufen.
Um eine normale Steuerung des Flugzeugs zu ermöglichen, soll durch die PTU aber dafür gesorgt werden, dass Grün und Gelb den gleichen Hydraulikdruck haben. Der Normaldruck beträgt auf allen Systemen 3000 psi (=207 bar). Ab einem Druckunterschied von 500 psi zwischen Grün und Gelb springt die PTU an zu arbeiten, und genau dann hört man dieses Bellen. Da die PTU im Hauptfahrwerksschacht sitzt, hört es sich so an, als wäre ein Hund irgendwo in den Frachträumen unter dem Fußboden eingesperrt.
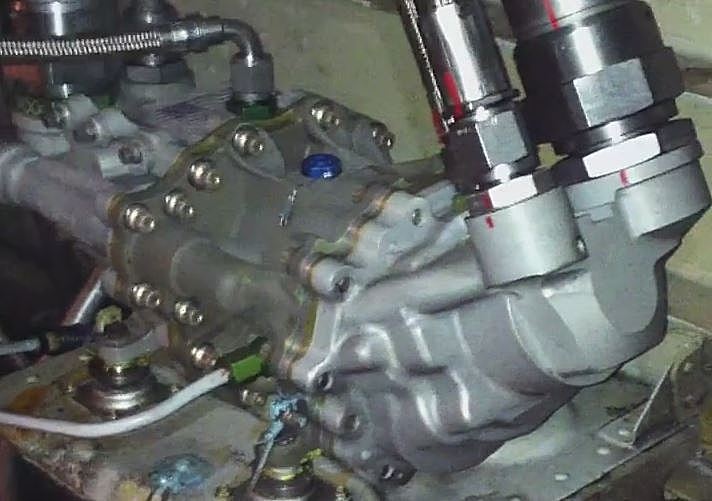
Wann hört man die PTU?
Man hört sie auf jeden Fall beim Starten der Triebwerke. Da beide Triebwerke hintereinander gestartet werden, ist für einen gewissen Zeitraum (nämlich zwischen dem Hochlaufen von Engine 2 und dem Hochlaufen von Engine 1) ein hoher Druckunterschied zwischen Grün und Gelb vorhanden. Dann springt sofort die PTU an und führt eine Art Selbsttest durch. Wenn beide Triebwerke laufen und beide Hydraulikkreisläufe durch die Engine Pumps auf 3000 psi stehen, geht auch die PTU wieder aus.
Nach der Landung wird bei vielen Airlines Engine 2 abgestellt, um mit einem Single Engine Taxi Kerosin zu sparen. Warum wird Engine 2 abgestellt? Ersterns hängt die Bugradsteuerung am grünen System (Engine 1 Pump) und zweitens hat das gelbe System ja eine elektrische Pumpe, über die es auch ohne laufende Engine 2 bedruckt werden kann. Wenn dann am Gate auch Engine 1 abgestellt wird und die Engine 1 Pump offline geht, verlieren die beiden Hydraulikkreisläufe sehr ungleichmäßig an Druck. Dadurch fluktuiert der Druckunterschied zwischen Grün und Gelb, bis irgendwann kein Druck mehr im System ist. Bis dahin aber arbeitet die PTU wie wild, um den Druckunterschied zwischen beiden Systemen auszugleichen. Während dieser Flugphase ist es nicht unbedingt nötig, aber die PTU macht halt ihren Job. 😉
Warum hört man das bei anderen Flugzeugen nicht?
Zwar müssen alle kommerziellen Flugzeuge dieselben Zulassungsvorschriften erfüllen, aber es gibt oft viele mögliche Systemarchitekturen und viele Wege Compliance zu zeigen. Die Boeing 737 hat beispielsweise nur zwei dauerhaft aktive Hydraulikkreisläufe (A und B). Das Standbysystem wird nur bei einem Fehler aktiviert. Zwar hat die 737 auch eine PTU, diese kann aber nur von System A zu System B Druck übertragen, um die Aktuatoren für die Leading Edge Klappen anzutreiben. Die PTU ist dort deshalb auch nicht so leistungsstark.
Beim A320 wurde nun einmal eine Systemlösung erdacht, die eine leistungsstarke PTU erfordert. Die ist dann eben auch entsprechend laut, aber bisher hat anscheinend noch niemand die Notwendigkeit gesehen, eine Neukonstruktion zu machen. Dann müsste man nämlich eventuell einen neuen Zulieferer finden, die Neukonstruktion durchführen und zulassen und man holt sich jede Menge Komplexität in die Ersatzteillogistik und Wartung rein. Da die PTU nur sehr kurz in Betrieb ist, wird sehr wahrscheinlich auch nicht gegen irgendwelche von Airbus gegebenen Kabinenlärmgarantien verstoßen.
Wenn euch irgendwelche Fragen auf dem Herzen liegen oder irgendwelche Themen brennend interessieren: Ich bin für Vorschläge immer offen!